Radon, the silent danger: Protecting Homes from Radon with Closed-Cell Spray Foam Insulation
13 Jul 2021
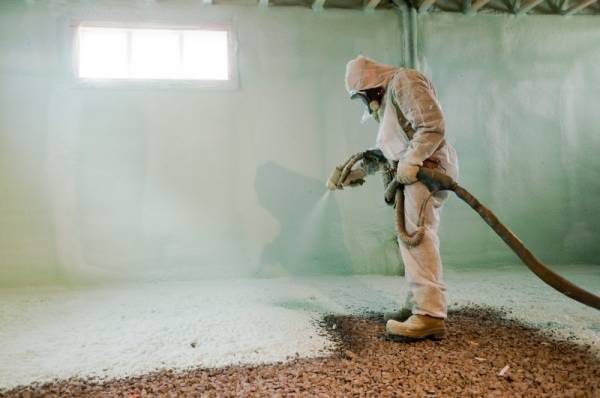
Across Canada, many homes have elevated levels of radon released from the soil. It’s odourless, tasteless, colourless and can enter homes and enclosed spaces through cracks in foundation floor and walls, construction joints, gaps around service pipes, support posts, window casements, floor drains, sumps or cavities inside walls. It is the number one cause of lung cancer in non-smokers and it’s silently killing 3,300 Canadians per year with lung cancer.
Canadian homes are especially a target as they are sealed against the various weather elements. Radon can become captive in the home and build up to dangerously high levels, causing harm to the DNA in our lung tissue with long-term exposure. November is Radon Action Month aimed to encourage Canadians to protect their health by testing for radon in their homes and reducing high levels of the gas. Health Canada estimates that about 16% of lung cancer deaths are related to being exposed to radon in the home. The adoption rates for radon testing remain low. A recent study commissioned by Health Canada found that only 6% of Canadians have tested their home for radon.
The Canadian government along with various partners, stakeholders and community leaders are committed to reducing the number of radon-induced cancer deaths in the country. Contractors and builders also play a lead role in educating homeowners and helping them address and control radon.
This year’s Radon Awareness Month emphasizes key municipal actions for the protection of homeowners against radon. Two impactful steps that involve the participation of the contractor and builder community are 1 – protecting homes while they are being built by considering building code measures that will control radon entry, and 2 – providing incentives to homeowners to work with contractors to install mitigation systems and get assistance in radon protection and/or removal through mitigation grants.
Active and passive radon measures
When it comes to radon, there are two basic types of mitigation approaches: 1-passive barriers defined as the collection of pipes and stack riser through the roof with no mechanical fan; and 2- active devices defined as a passive barrier system with the addition of a mechanical fan.
That said, all radon control measures must contain a depressurization zone (gravel) below the plane of airtightness. Once these have been installed, along with a connection to the occupied space, either a passive or active method is required to “move” the soil gas from below the slab to the atmosphere.
The nonpowered passive approach is when depressurization is developed through natural convective forces, such as a stack effect or positive pressure zone. The stack is extended up through the building shell and vents above the roof. When the air in the vent stack is warmer than outdoors, the air will naturally rise, depressurizing below the slab. The section of the stack that runs through the attic should be insulated to preserve the momentum of the stack effect, and a hardwired receptacle should also be installed to facilitate conversion to an active system.
The powered active approach is when an electric fan is placed in the vent, actively pulling air up through the stack and developing depressurization. Both active and passive methods must contain a continuous air-soil gas control layer and permeable material to create a depressurization zone.
How to determine radon levels in residential spaces
The only way to determine radon levels in a home is to test it after construction under normal occupied conditions. There is currently no reliable or affordable method to determine if a home will or won’t have high radon levels before its construction. Thus, justifying the code requirements to control the ingress of radon for all residential buildings.
Soil gas ingress is managed in new construction and renovations by 1- applying soil gas barriers to ground contact floors, foundation walls and roofs, 2- providing a gas collection layer (e.g. clear stone or gas mat) under all ground contact floors, 3- installing a piping system for the extraction of soil gas from under the floors, 4- sealing seams, cracks, penetrations and all openings in ground contact floors, walls and roofs; and 5- testing the radon levels in the building after construction. If the indoor radon concentrations exceed the Health Canada action level, the piping system can be connected to an extraction fan to control radon entry and exhaust the accumulated radon safely outdoors.
Some building codes do not currently mandate indoor radon testing after construction. “There is an entrenched belief that simply extending the continuity of the air barrier through the building foundation, as prescribed by the national and some provincial building codes, is sufficient on its own to control indoor radon levels. These views are contrary to the findings of Health Canada and extensive evidence and experience from relevant agencies in the United States and Europe.” Obtaining a perfect air barrier/soil gas barrier is virtually impossible using conventional construction methods such as sheeting and taping.
A cost-effective protection solution with HFO Closed-Cell Spray Foam insulation (ccSPF)
Considering the majority of soil gas intrusion is through air leakage (i.e. through joints, cracks, and penetrations) it is essential to ensure good sealing of joints, cracks, and penetrations and good continuity of the soil gas barrier. Through its ability to expand into crevasses and adhere to building elements, properly applied spray foam insulation can provide a continuous soil gas barrier, both under-slab and on foundation walls and roofs. It can also reduce construction deficiencies inherent to taped or caulked radon barrier system assemblies.
Reducing radon in the home can be done with spray foam insulation as a barrier from the ground up. There are new hydrofluoroolefin (HFO) based closed-cell spray foam (ccSPF) insulation products that have been tested for radon diffusion and are highly radon-resistant. Radon protection is usually provided by an air barrier material since radon travels primarily through the air. However, there can be radon diffusion through some air barrier materials. That is the reason why some ccSPF products have been tested in accordance with K124/02/95 (method C of ISO/TS 11665-13) for radon diffusion. At only 1’’, some HFO ccSPF performs 35 times better than a 6-mil (0.15 mm) polyethylene sheet for radon protection. Furthermore, these products are often installed at a thickness of 1-1⁄2” to 2’’ and are therefore much harder to puncture than 6-mil polyethylene when workers are walking on it during construction. Some HFO based ccSPF Canadian products have also been evaluated by a Canadian – National Radon Proficiency Program (CNRPP) (Radon Specialist) officer in Canada and have been characterized to outperform a polyethylene sheet for this application. ccSPF can be used as a substitute for the air/gas and vapor control layers and has a number of distinct advantages.
Typically, 1.5” of ccSPF is used to account for the unevenness of the gravel bed. Less than an inch is applied in the first pass to level out the substrate. Then a final application of 1” is applied on top of the preliminary layer. In this situation, ccSPF is being used for its barrier properties, but it also acts as insulation. A slab with 1.5” of ccSPF has an R-10 rating, which is sufficient for most code requirements for slab insulation. In most regions, 1.5” of ccSPF is sufficient to address the requirements for a subfloor vapor retarder. And of course, there are benefits to under slab insulation such as hydronic heating ready, elimination of cold concrete floors, energy savings through thermal mass effect, less floor cracking and condensation elimination to prevent mold growth. Other benefits of ccSPF as a radon control layer include:
It’s seamless: ccSPF provides seamless coverage of a surface. The continuity of the polyethylene barrier relies on the durability of the tape and the precision of its installation. Additional materials to complete the barrier like caulking or mastics can be eliminated, as well as termination edge failures and material compatibility issues.
It’s water-resistant: ccSPF takes a very long time to absorb water and if it does, once the source of water is removed, it dries out while being resistant to fungi. It also becomes a vapor retardant starting at 1.25’’ and is approved by the Federal Emergency Management Agency (FEMA) for use as insulation in flood zones.
It resists puncture: ccSPF can be walked on without puncturing it. When you lay polyethylene on gravel and then walk on it, which you must do to pour concrete, it gets punctured. ccSPF eliminates the need for repairing holes before the pour.
It exceeds requirements for air barriers: Air barrier solutions should be tested as systems to ASTM E2357, “Standard Test Method for Determining Air Leakage Rate of Air Barrier Assemblies.” The 6-mil (0.15 mm) polyethylene must be used with the tested tape to meet this requirement. ccSPF is commonly used as an insulating air barrier system in commercial construction. It has been tested as an air barrier system and gone through an additional durability test procedure to confirm its air barrier system test compliance after a full year of exposure to the Canadian climate.
It’s cost-effective: the application of ccSPF is very quick and when insulating the complete basement the production cost is lower per square foot since the applicator’s travel time and prep are offset by the volume to install, compared with a conventional insulation system that involves multiple steps, several materials plus more labour, which leaves more room for error.
Continuity or control layers
Spray foam insulation can be sprayed directly onto the prepared gravel substrate (minimum 1.5”) while aiming to achieve continuity between the insulation on the walls, rim joist and sub-slab. This area is one of the primary air leakage and thermal bypass areas.
Application rates vary depending on the complexity of the job, but to install both the air and vapour control layer and insulation in a 1000 square feet basement (wall, rim joist and under slab), it is usually completed in half a day. Compare that production rate to that of installing 6-mil (0.15 mm) polyethylene sheet, seaming and detailing all the penetrations, then insulating and seaming the insulation boards.
When it comes to the seal and self-flashing capability of ccSPF, each penetration is completely sealed, and the joint is insulated—no thermal shocking. The concrete and penetrations become part of the thermal envelope, which means the pipe is no longer subjected to thermal expansion and the concrete-to-pipe seal is permanent. The concrete becomes thermally protected and no longer subject to shrinkage resulting in cracks. The sump pump lid is also sealed.
Once the concrete has fully cured, interior finishing walls can be installed, and gypsum drywall applied. The foam cannot be left exposed and must be protected with an approved thermal barrier.
A good example using a hydronic heating system requires installers to walk on the surface for not only the rebar but also the heating system. The insulation and radon control layer remains in place with no punctures. Concrete is laid directly on top of the ccSPF surface. No additional vapour control layer is required. With no tape required for the structural framing members, the installation is completely sealed.
Retrofits for mitigation
Basement retrofits for radon mitigation can be completed with the addition of ccSPF as a radon control layer on the existing slab and a new second slab. The radon vent stack must penetrate both slabs and terminate within the permeable fill layer.
Existing floor penetrations can be sealed and insulated with the use of 1.5” of ccSPF applied directly to the existing concrete floor. At this point, hydronic heating can also be easily installed. If the designer or contractor wants to isolate the load-bearing wall, it is recommended to wrap plywood with commercial-grade air barrier material and install them before the second concrete floor is poured.
ccSPF can be applied directly to the original floor slab in a crawlspace, directly onto gravel and carried over onto the existing concrete slab floor. The spray foam will fully adhere to both surfaces. Retrofit applications can also be done over the original floor slab in a full basement. A total of 1.5” of ccSPF can be used, reinforced with rebar overtop with a hydronic heating system installed, and the application of concrete.
Caveat: ccSPF only works when installed by trained professionals
The continuity and durability of the control layer for radon abatement depend not only on the material used but also on the skill of the installer. ccSPF is installed by professionals who have been trained by the manufacturer and its third party for their specific system. In Canada, the training is provided by ISO-certified trainers, and then the installation is inspected by ISO-certified inspectors.
Author: Maxime Duzyk
Maxime Duzyk is the director of building science and engineering, North America with Huntsman Building Solutions. He’s been in the spray foam insulation business for the last 10 years.