Rethinking Spray Foam: D-Max Wall, innovative interior HFO spray foam application saves time, money without having to step outside
13 Jul 2021
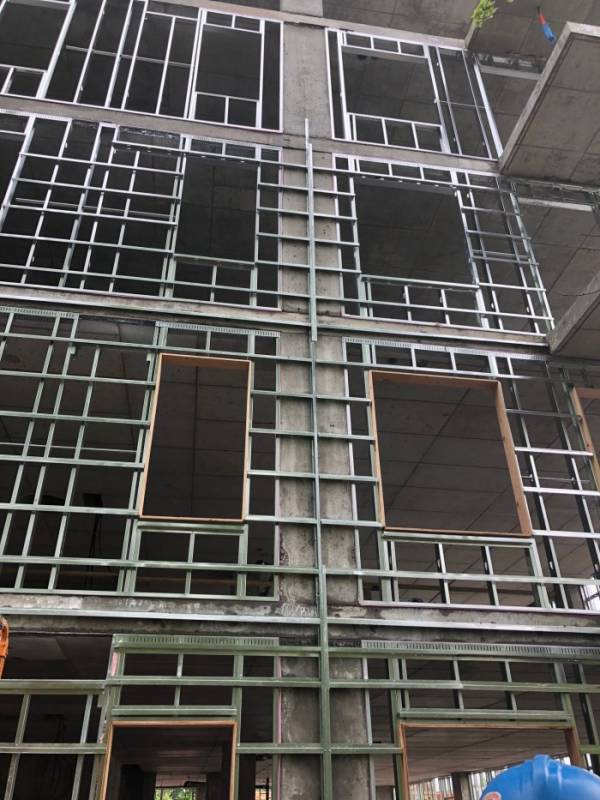
With the cold and wet Canadian winter upon us, architects, builders, and general contractors with large building projects on the go are most likely looking at ways to modify their work methods to the tougher below-freezing climate conditions so that they can ensure the success of their jobs and reduce costly winter construction delays. Adding to that, construction costs have also risen for all building types from the fourth quarter of 2019 to the first quarter of 2020. At the national level, construction costs during the first quarter were up for all types of residential and non-residential buildings with increases ranging from 0.4 per cent to 0.7 per cent (1).
When thinking about the insulation application process on the exterior of the building, with scaffoldings and weather conditions, it’s more difficult and costlier in the winter months than in the heat of summer. First-off when applying building envelope products in cold temperatures, while there are many steps you can take to ensure the successful application of the product, the job in the winter simply takes longer. Every single step of winter construction takes longer.
As such, climatic conditions are an important factor that should be considered when selecting construction products. They will be exposed to rain, snow, and wind and some other products will have their adhesion diminished in colder applications. This is not the case with spray foam.
There are so many considerations for successful winter application: temperatures must be constantly monitored; substrates should have less than 19 per cent moisture content; it might be raining too much, too windy, or there is just too much snow or ice on the substrate; and, as insulation products are often sensitive to water, the complete building needs to be watertight before installing the insulation, creating delays in sequencing. The exterior air barrier should also be applied before the interior insulation and the vapour barrier.
The bottom line, it’s going to cost more (time, labour and money) to install the building envelope in the winter than in the summer to a building project.
New Method of Spray Foam Application all Done From the Inside
There are some ccSPF products on the market that can be used to -20°C (-4°F) temperature, but even this is not enough to withstand some of our brutally cold winter days. What if you could use this same type of spray foam product in conjunction with an application method that eliminates the need to even spray from the outside? What if you could do it all from the inside?
For some recent building projects in Quebec, the architects and general contractors involved have done just that. Projects such as Saint Philippe, led by architect Bilodeau Baril Leeming and general contractor Dinamo; the Nicolas build led by Beaudet Faille Normand and Dinamo; and the K Building led by Alpha Architecture and Dalcon. All these projects have taken on a new spray foam application method where everything is done from the inside. There’s no need whatsoever to step in the outside cold to apply spray foam.
The D-Max Wall method is a new way to build. The D-Max Wall application method is done in combination with a ccSPF product, where the wall is composed of regular steel studs; but instead of installing the exterior sheeting directly on the steel studs, a Z girt is installed horizontally on the studs and then the sheeting is installed on top of the Z girts. This will create a space between the studs and the sheeting, which allows the foam to insulate between the two and removes the thermal bridge. It’s as if the insulation is on the exterior of the structure, when it’s actually applied from the interior of the building.
A ccSPF along with this new application method removes the need for the spray foam applicator to work outside, leaving other building envelope trades to work faster on the exterior of the building and to complete their part of the building project. It saves you on the time spent onsite, is more economical, and provides a higher building envelope quality and durability.
The spray foam used in the interior application replaces four materials including the exterior insulation (rock wool or others), the full-surface membrane, the fibreglass insulation in the cavity, and the poly. Because spray foam acts as an air barrier, vapour barrier, and insulation, it can replace all of these materials, is not affected by water (so it can rain or snow on the product without there being a need to replace it), and is also mould resistant.
The D-Max Wall application method makes winter construction much easier. It can be as cold as -20°C outside and you will still be able to apply the ccSPF as soon as the first floor has had the exterior sheeting installed. And, as the product is resistant to water, there is no need for the building to be completely watertight to apply the ccSPF. This will save on heating costs during construction since the insulated floor can be heated right away. In addition, there is no need to have heating without insulation, which often creates condensation or frost issues and there’s no questioning which products should be installed first; there is only one product to install. Finally, a complete set of detailed drawings is available to facilitate the design and construction of these projects. The assembly is certified by an engineer and tested to meet the building code requirements for high-rise buildings.
Benefits of the D-Max Wall Assembly vs. Traditional Assemblies
D-Max Wall assembly is getting a lot of traction with building projects as it can easily meet the new insulation requirements regarding U-value or effective R-value, and it can be done with an HFO based ccSPF product. It has also been rated for two hours of fire resistance between floors by fire resistant products manufacturers.
Other benefits include:
- Can be sprayed regardless of temperature or wind (up to -20°C).
- No scaffolding or vessel necessary. Less machinery; therefore less rental cost, logistics, and risk of accident.
- Building insulation can be performed as the walls go up.
- Less materials therefore time and cost savings for execution.
- Heating cost savings in winter.
- Avoids exterior compartmentalization (NBC Article 3.1.11.2.).
- CAN/ULC S101 tested assembly for high rise buildings (greater than three storeys) (UL EW25).
- Sequencing of work is simpler and easier to manage for the superintendent, since there are less workers to execute each step.
- Avoids overspray.
- Avoids having to install an interior furring in comparison with a fibreglass insulated cavity where the electricity cannot run through the stud cavity.
Every building project must address thermal performance, air leakage control and moisture management in order to provide a healthy, economical, durable living space. The D-Max Wall application with ccSPF provides this to those living and working in these indoor spaces. And for those on the work site, it provides much more when successfully applied by a qualified and certified ccSPF installer, as well as offering greater time and labour efficiency and budget savings.
Author: Maxime Duzyk
Maxime Duzyk is the director of building science and engineering, North America with Huntsman Building Solutions. He’s been in the spray foam insulation business for the last 10 years.